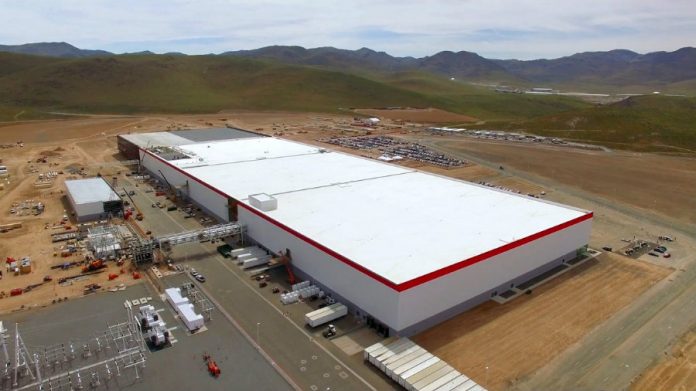
Reno – In a room of what’s to be the biggest building in the world, Elon Musk, CEO of Tesla Motors Inc. (NASDAQ: mayTSLA) confirmed the final design for the company’s $35000 Model 3 were finished two weeks ago. Now, the automaker is moving forward to build the Gigafactory 1.
The Gigafactory opened the doors on Tuesday, and its schedule is being pushed so Tesla can produce 500,000 Model 3 sedan in 2018.
Musk, 45, said Model 3 might bring a revenue of $20 billion a year, with a 25 percent of profit margin. Meanwhile, Tesla has a 10-year plan that will cost “tens of billions of dollars” to implement.
As big as New York’s Central Park
Gigafactory 1, the battery factory in Nevada, is a crucial part Teslas’ ambitious program. But, so far, it only half a small fraction of the giga-size its supposed to have and executives hopes the factory can raise the production line 10-fold by 2018.
When completed it will be a three-story building about the size of New York’s Central Park. Or, to make a more comprehensive image, 107 football fields put together in Reno, Nevada.
Gigafactory 1 will handle every aspect of the battery packs, while the auto factory remains in Fremont, California, 240 miles away. Tesla plans to build a train line connecting both places so raw materials can be shipped back and forth.
By the time the facility is fully functional, the Gigafactory will be powered mostly by onsite solar panels backed with batteries. Tesla already has capped the natural gas line leading to the factory, so there will be no going back to fossil energy.
Panasonic’s involvement and the battery issue
When Panasonic Corp (NASDAQ:PCRFY) was first introduced to the idea of Tesla’s Gigafactory, a couple of years ago, they deemed it crazy. Still, Panasonic agreed to become partner in the endeavor and is now aiming to create 500,000 car batteries for 2018, a plan that cost Tesla at least $5 billion and that has already seen 400,000 deposits to buy the upcoming Model 3.
The company is gambling $1.6 billion on the quest. So far, they’ve been working in their factories in Japan, but soon those efforts will cross the ocean towards Gigafactory.
Under the partnership, the Asian tech giant will install its own equipment, manage its employees and sell the battery cells to Tesla. Gigafactory employees from both companies, however, will work as a single enterprise.
Currently, 1000 employees are working in the factory to deliver the first batch of batteries later this year. Eventually, 10,000 people will work there. The batteries are lithium-ion cells larger versions of AA batteries. Model 3 will use thousands of them, packaged in a tight space. This technology is new for every automaker.
Batteries tend to make up a third of the price of an electric car and are the single reason these eco-friendly vehicles are more expensive than their gasoline counterparts. Musk is confident this component will reach a price of $100 per Kilowatt hour by 2020, down from an average of $1200/kWH in 2010.
#Tesla opens #Gigafactory doors for a #firstlook https://t.co/AXZX7oL8z5 pic.twitter.com/Nwcmxl1SCC
— inhabitat (@inhabitat) July 27, 2016
If he is right, the electric-car market will shift, and batteries prices are already falling due shorter supply chains and factory automation.
Source: NBC News