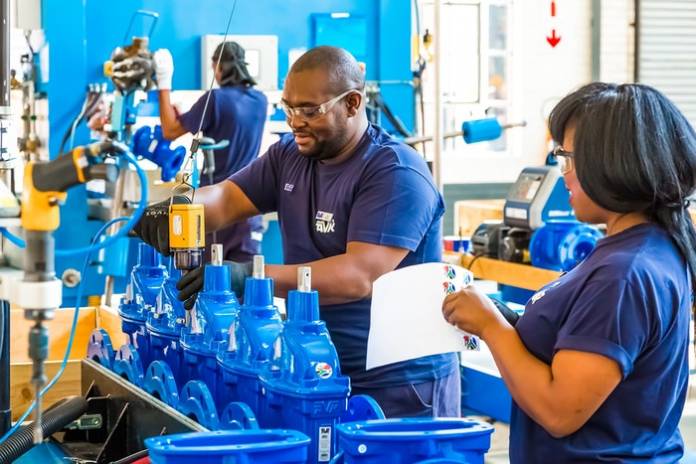
Come every new year, apart from looking into your business plan, it’s always a good idea to relook your business processes, the systems that are in place, and introduce new habits to the way you manage and manufacture things. All of this is just another way of developing and enhancing your business to achieve operational excellence.
Above all, refining these processes time and again ensures better management of time and resources, reduce operational costs, improves the quality of your products, and enhances your staff’s productivity. This, in turn, will lead to increased profits and sales, not to mention a more positive brand image.
Here are ten ways to improve your manufacturing habits and processes to transform your business in 2020:
1. Engage the entire team and workforce.
When things are unpredictable, it helps to enable a two-way channel of questions, queries, and answers. Your workforce will have plenty of concerns and issues with the processes at work, and it only makes sense to relook into these concerns and address them to improve efficiency. Different levels of the supply chain will have a different outlook on the business process. Engaging your workforce time and again will help you, the business owner, identify smaller opportunities for change to make things better for the workers and top management.
Solving smaller issues and problems will help your business run more smoothly. It also increases the motivation of those working on the shop floor. They will have a sense of belonging because you’re giving them a voice to address their concerns. Opening up the communication channel is more effective than the traditional method of having information flow from top-down.
2. Be transparent about expectations.
If something goes wrong in the production line, or your business hasn’t met its targeted goals, there could be something wrong in the communication between the business goals and what’s expected from the workforce. Have you communicated what’s expected from your team? If not, you can’t blame them if business expectations aren’t met. Not clearly identifying priorities and goals leads to employees spending a huge portion of their workdays accomplishing the wrong objectives. Creating realistic and clear goals is what makes a better manufacturing process.
3. Giving employees the right training
Investing and providing the right kind of training, the right kind of software, and the right kind of tools to help your employees do a better job is necessary for a clearer and smoother manufacturing process. Investing in software such as fishbowl manufacturing software is one of the best things you can do to ensure you give your employees the tools they need to handle multiple sales tasks, inventory, and streamlining workflow, especially if your manufacturing process hits a logjam.
4. Opening up the floor for changes
As a business owner, you need to be open to changes, and that also means encouraging your employees to make small changes in their work systems and processes. Allow them to experiment better ways of making their job faster and easier. This not only boosts morale but also reduces micro-managing and fosters a stronger sense of trust among the different levels of management and the workforce. Better morale leads to higher productivity and increased efficiency.
5. Better waste management
2020 should be the year to look into controlling waste and better management of resources. If you haven’t done this already, the time is now. Better waste management isn’t only materials, but also time and labor-intensive processes. Cut down on inefficient processes, on using too much material when possible, and on time taken to complete a project. Relooking your manufacturing processes also means relooking into the waste you’re producing. You want to reduce time, effort, and material waste because this contributes to a healthier bottom line.
6. Relook the way you plan your office space.
Once in a year, it’s always a good idea to KonMari your office space, too. This entails being organized, managing the workspace to identify where certain tools are kept, where materials are stored, and where resources can be obtained to make it easier for every worker on the floor. Workspaces should be free of debris to minimize health and safety risks. Not only is it a potential hazard, but it can also be a loss of money and time for people to find what they need to get their job done.
7. Keep track of your suppliers.
Part of reconfiguring or cleaning up your manufacturing process also means looking into your list of suppliers. Which supplier has brought the most value? Which supplier is the easiest to work with? Which supplier has the best quality and value for money? It’s a good time to get rid of suppliers that haven’t met your business objectives and look for new suppliers with better technology and quality. You also want to work with suppliers that have a better and more positive attitude. Those who display a willingness to put you first will likely be quicker to respond should there be any problems or if you need help.
8. Get feedback from your customers.
Keep communication lines between your brand and your customers open. You want their ideas, as this is a significant source of innovative ideas for improving your product and solving your customer’s pain points. Just because you don’t get complaints doesn’t mean there’s no room to improve and make things better. You must always look into developing your product or service to stay ahead of the competition and to meet your customers’ needs. If these ideas from your customers mean a little bit more work for your employees, this will eventually lead to higher revenue. Receiving customer feedback also means you have a better brand reputation because you’re willing and open to receive feedback and improvement ideas.
9. Standardize your workforce.
Every operation at every level in your production line needs to be standardized to achieve maximum efficiency. Train your team, put SOPs in place, and give them the right tools and software to log in information, send emails, record information, and update details. Doing so will result in more consistent quality, optimum production, and less downtime.
10. Continue to always reinvent.
As the years go by, technology will dictate the next best thing, and being in any business means you must always stay ahead of the game to be competitive. Continuously being open to improvement, to receive feedback, and to adapt are among the key elements in ensuring business sustainability and profitability.