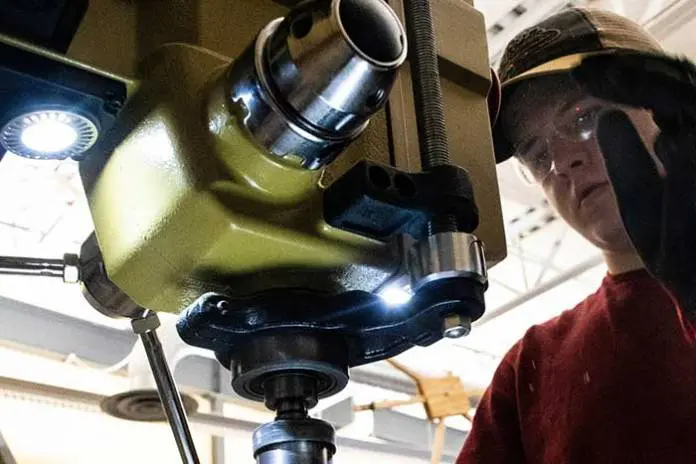
Many industries have adopted manufacturing automation over the past few decades. Today, the manufacturing industry sits on the knife-edge of automation technology, much ahead of other sectors. The manufacturing industry has revolutionized how industries perform their operations and activities.
However, as industrial automation increases, the involvement of human beings in production is reducing at a significant rate. Without human limitation, machines have been able to get work done faster and with greater precision, thereby increasing the quality of products produced.
Despite changing the nature of employment in many companies, manufacturing automation has brought other profitable opportunities to the industry.
Collaborative Robots
One of the most popular types of manufacturing automation is the collaborative robot. The collaborative robots are programmed to operate around the clock in all situations to assist manufacturing companies in increasing their production capacity, performance, revenue, and throughput.
Another reason manufacturing companies adopt automation through collaborative robots is that these robots can make independent judgments and decisions. They can be made more versatile to take up more tasks that require creativity as the underlying technologies advance.
Uses of Collaborative Robots in Manufacturing Automation
Packing, picking, and palletizing
Packing picking and palletizing are production activities that need a high level of accuracy when being performed. Manufacturers are finding collaborative robots more convenient to use than human beings because the human resource finds the large-scale production tedious, hectic, and time-consuming.
The use of collaborative robots in manufacturing has also reduced the chances of making mistakes during production. While humans make mistakes while working, the probability of machines making a mistake is much lower.
Errors in the work process reduce the quality of goods produced and consequently affects the revenue system. For example, if a mistake was made during product packaging and a customer receives the wrongly packaged product, the customer’s rating of the company will reduce drastically.
These errors negatively impact the level of customer satisfaction, thereby reducing sales and profits. If such a company changes the mode of production from human to machine-based, it could reverse these adverse effects and change everything for good.
Moreover, Collaborative robots are designed to work with humans. They reduce the workload of employees by sharing their workload.
Another significant advantage of using collaborative robots to automate the manufacturing process is the speed of production. Collaborative robots have the potential to function 24/7. They can work for more days and longer hours, unlike humans.
Robots have advanced intelligence. They can pick different items and categories them according to the sequence required for constructing a specific product. They can also package them into different packaging and also palletize them.
Manufacturing companies with automated production can now achieve higher production targets at a faster rate. Due to lack of errors, the time used to complete production processes is tremendously saved.
Advantages of Machine automation in Picking, Packing, and Pelleting:
- Reduced error
- Increased quality of work
- Increased customer satisfaction
- Reduced workload for humans
- Increased speed of production
- Higher production targets are met, and more revenues are made.
Welding
Every successful manufacturer aims to produce high-quality goods that meet customer expectations at the least possible cost. Due to this reason, many manufacturing companies are striving to accomplish this goal by acquiring and applying advanced technologies. One of the most commonly adopted technologies in the welding sector is the use of collaborative robots.
Welding and soldering in manufacturing are cumbersome processes. Although human resources can do these tasks, they cannot perform them over a long time. Manufacturing companies cannot keep employees working all day long. Hence, the majority of companies are adopting the use of collaborative robots to reap long-term benefits.
It is important to note that although transitioning to a robot setup is capital intensive, it benefits significantly to compensate for the investment.
For example, the sensing capabilities of robots are enhanced computer vision and sensor systems. This potential enables robots to sense disastrous environments and notify and advise workers on the best way to handle the situation beforehand to save resources and save both time and lives.
Advantages of Automation in Welding
- Error-free production
- Increased rate of output and higher revenues
- Uniform high-quality products.
- Reduced wastage.
Assembly
Assembly is part of the production processes in manufacturing. It involves the assembling of different elements to form a whole product. Although this process may not be time-consuming, depending on the product being manufactured, however, it can be quite a tedious task for human beings.
Besides, human beings are prone to make errors while assembling a product. Assigning collaborative robots will eliminate the chances of error and reduce the human proximity to large equipment that compromises their safety.
Collaborative robots now have advanced programming. They can cater to the manufacturer’s business needs with appropriate guidance. For example, image-processing abilities and vision-enabled sensors enable collaborative robots to sense when a human enters a work area.
The robots respond by reducing their speed and continue to operate at high speed when the worker exits the premises. This ability reduces the chances of industrial injuries.
Advantages of machine automation in Assembling
- Elimination of errors
- Enhanced work safety.
Material Handling
Material handling is one of the most common tasks in companies today. It’s a tedious task for humans that needs to be accurately handled to meet customer expectations. Hence, companies need to automate repetitive tasks such as handling materials.
One of the best ways to deal with this issue is to introduce collaborative robots inside the company. Collaborative robots easily quickly understand the requirement of each task and work at a faster speed than human capital.
Additionally, collaborative robots also provide hazard-free work environments by automatically clearing all.
Advantages of Machine Automation in Material Handling include:
- Reduced cost of production
- Increased worker safety and health
- Reduced downtime
- Faster cycles of production
Final Takes
Complete manufacturing automation with robots such as collaborative robots is the future of production. Robots produce error-free work, increase the quality of products, reduce production costs, faster cycles of production and lower downtime, and increased worker safety. Machine automation is the key to increased production targets and generated revenues.