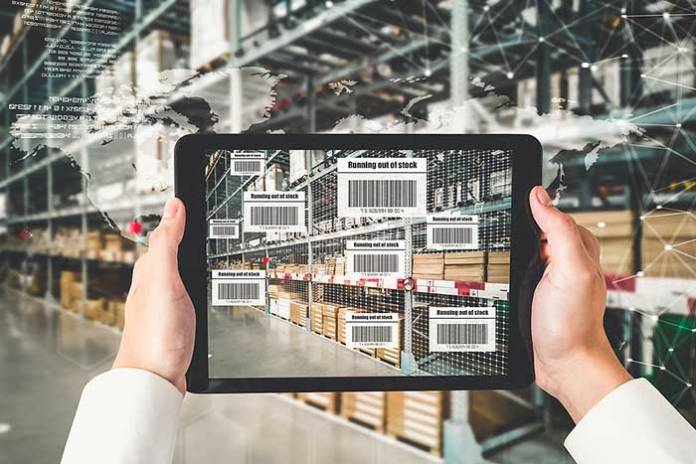
Kanban is a method of workflow management that more and more companies are starting to pick up on, one that can apply to nearly any business. It fits into almost any industry and can have a range of useful benefits, but what is it, exactly? More importantly, how can you use it for your own business?
What is the Kanban system?
Kanban comes from the Japanese term for ‘billboard’ and is focused on using a columned system to keep track of how different projects are progressing. While there are multiple ways to handle it, the idea is that you use cards to keep track of each project or event that a team is working on, tracking each major stage.
Common Kanban boards are designed with at least three columns: “to do,” “doing,” and “done.” In a business environment, you can add as many as you need, whether that covers testing or individual stages of a production line. When a project moves to the next stage, you move its icon or card to the next column.
How does this help?
While this might seem pointless at first, Kanban is great for visualizing a particular task. For example, in an industrial fastening products industry, you might use this system to keep track of raw materials and tools as they are delivered. Through this, you can identify shortages, then look into the stage that the materials are stuck at to figure out why those shortages are happening.
The more granular and focused a Kanban board is, the better it becomes for these situations. When every single stage is represented on the board, you can find out where the bottlenecks are, making it a lot easier to focus on problem areas that are slowing your entire business to a crawl.
What else is Kanban for?
While Kanban is a very basic concept, once you understand the idea behind it, it can serve a huge range of different roles. Whether you use it on a personal level or as part of a larger business plan, it can be a direct upgrade to the usual ways of tracking if a project is complete.
On-Time Production
A major part of any production line is having the right equipment, components, and materials available at the right time. The Kanban supply chain makes logistics a lot easier by placing responsibility on the right people at the right time but also speeds up the gathering of those components too.
For example, when you need industrial fastening products, you may need two screw X and one screw Y for each item on your production line. However, since they serve different purposes, having a lack of either stops your production line dead. With a Kanban system, these items can be collected and handled step by step.
Improved Logistics
Logistical changes to a business can sometimes be risky. The way that Kanban is set up means that it can be added on top of your usual operations without needing to worry about delays because the main thing that changes is how each step is tracked. As long as employees and contractors can update the system properly, it can work almost immediately.
There is not a one-size-fits-all way to handle the logistics of an entire company, but something like this can at least be modified quite heavily to serve the purpose you need. It does not even have to be the same system throughout the entire company: you could choose to only use it in certain projects.
Inventory Size
Having an effective ‘just-in-time’ delivery setup (and optimizing it properly) means that you will not end up with an excess of one item and a deficit of another. By tracking each stage and knowing where the bottlenecks might be, you can adjust the overall plan you are following to try and minimize how many things you are keeping in storage that you can’t use on their own.
This is especially important with niche components or items that you can’t re-use for many other purposes once you have them. An overflow of a specific car part is something that you either have to re-sell or keep in storage, limiting your available space for more important items that you do need.