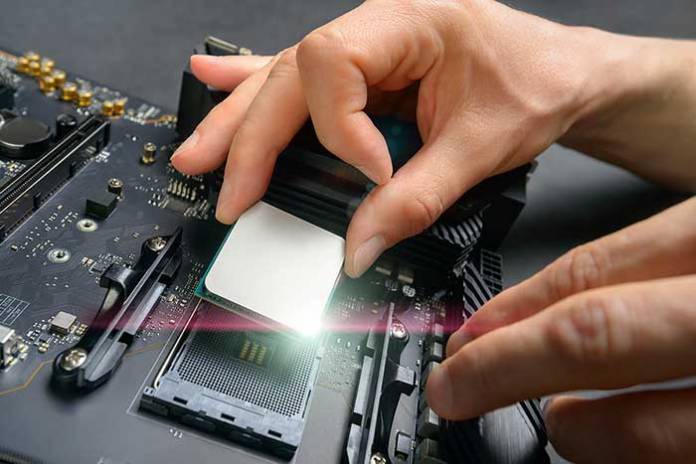
As a manufacturer of complex electronics such as cellphones, computers, and televisions, you are quite aware that hundreds or even thousands of parts are required. You may, for example, frequently purchase numerous Nvidia microelectronic products, for example. But what happens if you experience a part shortage in your supply network? Take the following steps to prevent this from happening.
MAKE PLANNING A TOP PRIORITY
It may sound too simple to even emphasize, but accurate materials forecasting is often a casualty for busy manufacturers eager to get finished products out the door. On-the-spot forecasting requires a laser focus on measuring previous production and sales benchmarks and then doing your best to make educated decisions based on them. Modern analytical software can be a godsend for procurement teams interested in refining their knowledge about past supply chain usage, but human collaboration must take place as well. Never underestimate the value of person-to-person conversations to get to the bottom of questions and sort out anomalies.
MAKE YOUR SUPPLIERS FULL MEMBERS OF THE TEAM
Speaking of human interaction, the businesses that provide you with the raw materials and components you require are just as important as your in-house employees. Treat them with the respect and inclusion they deserve by involving them in your communications. To that end, share your overall supply chain strategy with them, including how you plan to measure performance. On a regular basis, host face-to-face meetings were issues, including potential threats to materials acquisition, can be discussed and ironed out and brainstorming can take place. Even when you are not in the same room or even on the same continent, set up regular video conference calls to give everyone a chance to stay in touch.
WIDEN YOUR FOCUS TO ENCOMPASS MORE THAN COSTS
When you put money above everything else in your supply network, you may end up with lower-quality products, lags in supplier responsiveness, and increased lead times. Frugality has its benefits, but so does the best-value sourcing approach, which takes numerous factors into consideration when calculating the total cost of ownership (TCO). Additional elements to keep in mind when employing this approach can include lead times, supplier flexibility, the risks a supplier represents, and the vendor’s commitment to improve and change with altering conditions.
Creating a supply chain that is flexible and resilient represents an ongoing challenge for manufacturers of all sizes. The degree to which they succeed often determines the likelihood that part shortages occur as well as their severity and impact on the business. By emphasizing planning and communication and paying attention to more than just costs, organizations can design a supply network that will meet their needs now and into the future.