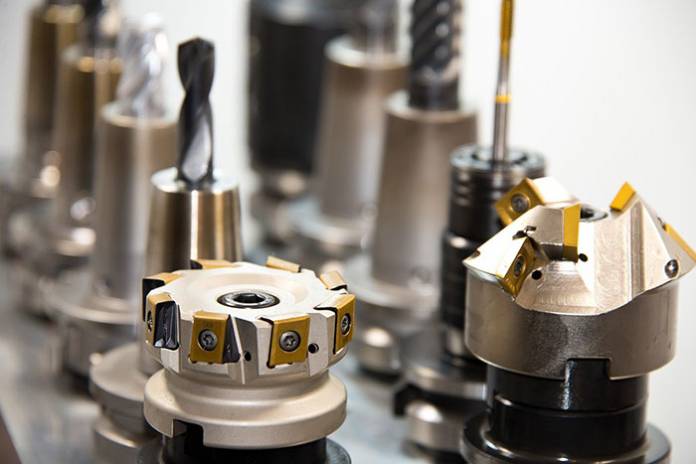
Since the 1800s, history has been witness to three industrial revolutions. Each of these industrial movements has been driven by disruptive new technology. The mechanics of the steam engine, the innovation of the assembly line, and the speed of the computer have all brought about modernization and drastic changes to the industry. The reason they were called industrial “revolutions” was that the innovation that powered them completely revolutionized how goods were produced and how work was done. They didn’t just improve productivity and efficiency slightly. We’re now witnessing a fourth Industrial Revolution that’s known as Industry 4.0. This new wave of digital technology takes the automation and computerization from the third industrial revolution into the future.
Industry 4.0 is driven by the Industrial Internet of Things (IIoT) and cyber-physical systems. They’re smart, autonomous systems that utilize computer-based algorithms to monitor and control things like machinery, 3d printing, robots, and vehicles. Industry 4.0 makes everything in the supply chain “smart.” This is everything from creating things from smart manufacturing and factories to smart warehousing and logistics.
Changes to the supply chain are only the beginning of the impacts being felt by the Industry 4.0 movement. This movement is also making connections with back-end systems, like enterprise resource planning, to give companies an unparalleled level of visibility and control. Ultimately, Industry 4.0 is a major part of any company’s digital transformation. Let’s take a look at how Industry 4.0 can make a big impact if businesses are ready to embrace it.
Collaborative Technology
Industry 4.0 is built around nine areas of technology. Data and AI analytics, horizontal and vertical integration, cloud computing, augmented reality, industrial internet of things, additive manufacturing and 3D printing, autonomous robots, simulation, and cybersecurity are the pillars of this new industrial revolution. These innovative instruments bridge the physical and digital workplace and make smart and autonomous systems a reality. Businesses and supply chains already use some of these advanced technologies for production and product development, but the full potential of Industry 4.0 comes to life when they’re on a higher level together.
It’s estimated that only about 13% of businesses have fully realized the impacts of their industry 4.0 investments, enabling them to achieve cost savings and create growth. As an example, technologies like 3D-printing can allow manufacturing companies to print their own parts, which can transform product quality at a lower cost and faster than traditional processes. Companies that aren’t taking advantage of the optimal mix of cyber-physical systems and technology are missing out on billions in profits. The implications of this collaboration of technologies can increase productivity and revolutionize the entire production process from start to finish. This industrial revolution is bringing together technology to make your business work smarter, not harder.
Smart Factories
Smart factories could change the future of manufacturing. Since the first industrial revolution, the pace of change in the manufacturing industry has been focused on producing products as efficiently as possible. Industry 4.0 can create highly digitized, largely autonomous facilities that take full advantage of advanced communication technologies like artificial intelligence, robotics, analytics, and IoT.
Also known as factory 4.0, these smart factories of industry can be self-correcting, apply smart manufacturing processes, and make it possible to deliver customized products cost-efficiently and at scale. The smart factory embodies a leap forward from more traditional automation to a fully connected and flexible system. The fourth industrial revolution has created factories that can use a constant stream of data from connected operations and production systems to learn and adapt to new demands. The results for your business can be a more effective and agile system, less production lag, and a greater capacity to predict and adjust to changes in the facility. All of this could lead to better positioning in the competitive marketplace.
Empowered People
No matter how autonomous smart factories and systems get, there will always be a need for people. Industry 4.0 can empower employees with technologies like artificial intelligence and live sensor data. Being well-versed in these new technologies will ensure that they know what’s happening on the manufacturing plant floor and are also ready to make quick decisions to handle issues as they arise. Wearable digital technology and augmented reality apps will help them solve problems, monitor their health, and keep them safe. This new technology can take your employees to the next level of productivity and engagement.
Incorporating industry 4.0 digital technology into your business can take time and effort. The benefits of this technology, however, can be huge for businesses that use data to make strategic decisions. This new way of doing business can revolutionize production, profits, and markets and change the future of manufacturing.